Particles in Aluminum 7075-T6
Paul Kern and Chris Shartrand
03 00 AM ,Wed, Sep 16 2015
Background Knowledge
- Aluminum Alloy consisting of Zinc, Magnesium, Copper, Iron, Silicon, Manganese, Chromium, Zirconium, and Titanium.
- During processing it is common for μm-sized particles to become ingrained in the matrix
- Deformation can cause particles to become cracked or detached
- Cracks combined with stress can lead to failure in the alloy
Importance
- AA7075 is commonly used in the construction of airframes
- Product failure = Costly
- Improved modeling can lead to prediction of microstructures that have a higher probability of cracking.
- Quantification of product quality.
The Microstructure
- Particles are very stiff
- Tend to cluster and form “stringers” along the direction of the roll
- Use Pair Correlation Functions (PCF) to quantify probability of finding another cluster from a given point
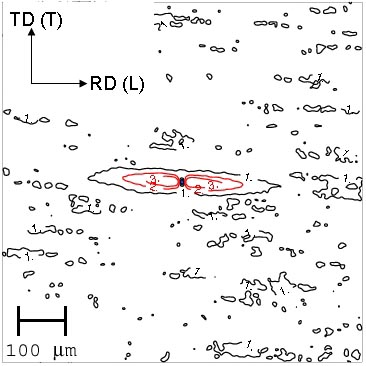
Microstructure Property
- Fatigue Indicator Parameters (FIP) are used to quantify damage
- We will use the Fatemi-Socie FIP: $FIP_{FS} = \frac{\gamma}{2} ( 1 + k\frac{\sigma}{\sigma_y} )$
- An elastic-plastic constitutive model must be defined
- We are using a linear-elastic model for the stiff particles with: Young’s Modulus of 169 GPa and Poisson Ratio of 0.3
- Investigating the non-local averaged FIP surrounding the particles
- Averaging volume of ~5% particle volume will be used
Simulation
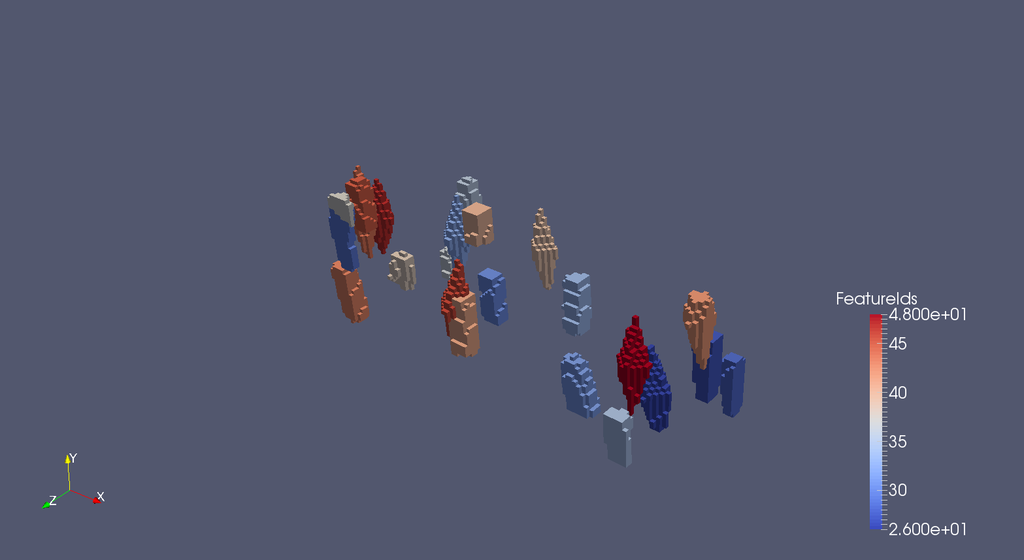
Two-Point Statistics
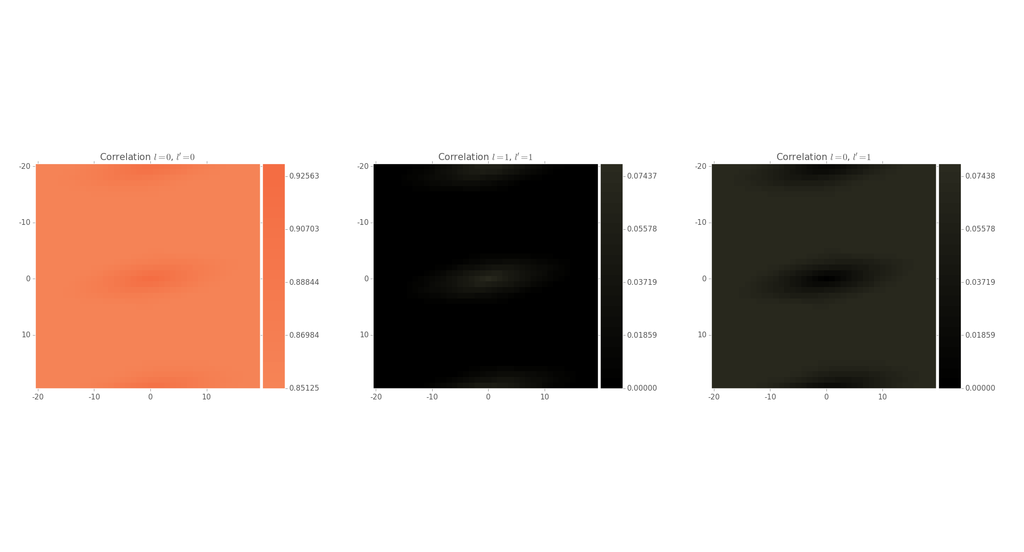